What are Spiral Wound Gaskets?
What are Spiral Wound Gaskets?
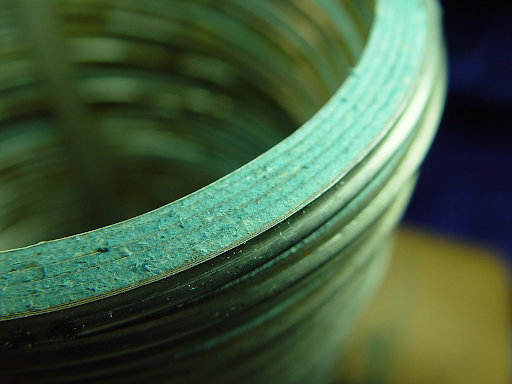
Early in the 20th century, the spiral wound gasket was created to withstand the increasingly tricky operating conditions in oil refineries. A flexible and resilient rubber gasket is required due to the fluctuations above, the temperature differential across the flange face, and bolt stress relaxation. It is impossible to overstate the necessity for the gasket to rebound from shifting conditions.
Here mentioned are the information about spiral wound gaskets
Color coding
Every
spiral wound gasket is color coded. The colors of the outside rim and the stripe along the edge give information about the material of the gasket components. The color of the outer rim indicates the material of the gasket's winding. In contrast, the fabric of the gasket's filling is indicated by the color of the rim strip.
Edge sealing
Since most gaskets are made of sheet material and have flat surfaces, they seal well. The space between flanges that differs when they are not parallel necessitates using thicker material. The material must compress more where the gap is narrower. The material quickly reaches its technical limitations. The spirally coiled gasket, in contrast, seals on its edges as opposed to a flat surface. To do this, a ring is made by twisting a long, thin strip of gasket material. The sides of the strip form the seal when positioned between flanges.
Built-in spring
The gasket material is interleaved with a metal strip to offer elastic recovery, ensuring that a seal is maintained regardless of how the joint moves. The mixed materials are roughly shaped into a V during the coiling process. The metal V pushes outward against the flanges like a spring. It is used in hydraulic cylinder seals.
Gasket construction
A spirally wound, V-shaped stainless-steel strip plus a non-metallic filler material, such as graphite or PTFE, make up the semi-metallic spiral wound gasket. A solid outer ring part of the gasket is also used for centring and managing compression. By not overtightening, the possibility of material creep is reduced. Spiral wound gaskets
with an additional inner ring are available for the most demanding situations. By doing this, the windings, mainly the filler, are shielded from contamination or damage caused by products that pass through the pipeline connection.
Types:
Different varieties of rubber gaskets are available. Examples of common spiral wound gasket types include the following:
- Style CG:
This spiral wound gasket has an outer metal ring and a sealing component. The outer ring delivers the best sealing results by preventing over-compression. The crew also makes it easier for the gasket to be placed on the mating flange faces.
- Style RIR:
It consists of an inner metal ring and a sealing component. The inner circle creates a physical barrier between the sealing element and the media stream and serves as a compression barrier.
Bottom line
Ask if a spiral-wound gasket would be a good choice if you have a complex junction to seal. Before disassembling the joint to replace a spiral-wound gasket, check the color code and place an order for the new item. A
hydraulic cylinder seal
also requires a spiral wound gasket.